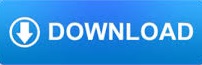

¨ when the arc is projected on the selected plane, the distance from the current point to the center differs from the distance from the end point to the center by more than 0.0002 inch (if inches are being used) or 0.002 millimetre (if millimetres are being used). In this format, it is OK if the end point of the arc is the same as the current point. In the center format, the coordinates of the end point of the arc in the selected plane are specified along with the offsets of the center of the arc from the current location. In both formats the G2 or G3 is optional if it is the current motion mode. We will call these the center format and the radius format. Two formats are allowed for specifying an arc. If cutter radius compensation is active, the motion will differ from the above see Cutter Compensation. Lines of this sort are hardly ever programmed.
#Mastercam x4 hole plane code
If a line of code makes an arc and includes rotational axis motion, the rotational axes turn at a constant rate so that the rotational motion starts and finishes when the XYZ motion starts and finishes. If the arc is circular, it lies in a plane parallel to the selected plane. The axis (or, equivalently, the plane perpendicular to the axis) is selected with G17 (Z-axis, XY-plane), G18 (Y-axis, XZ-plane), or G19 (X-axis, YZ-plane). The axis of the circle or helix must be parallel to the X, Y, or Z-axis of the machine coordinate system. the conventional four quadrant conventions).Ī circular or helical arc is specified using either G2 (clockwise arc) or G3 (counterclockwise arc). X~ is the radius of the line from the G16 polar origin and Y~ is the angle in degrees measured with increasing values counterclockwise from the 3 o’clock direction (i.e. (b) If G16 has been executed to set a polar origin then linear motion at feed rate to a point described by a radius and angle G0 X~ Y~ can be used. This will produce co-ordinated linear motion to the destination point at the current feed rate (or slower if the machine will not go that fast). The G1 is optional if the current motion mode is G1. (a) For linear motion at feed rate (for cutting or not), program G1 X~ Y~ Z~ A~ B~ C~, where all the axis words are optional, except that at least one must be used. If G53 is programmed on the same line, the motion will also differ see Absolute Coordinates.

the conventional four quadrant conventions).Ĭoordinates of the current point at the time of executing the G16 are the polar origin. X~ is the radius of the line from the G16 polar origin and Y~ is the angle in degrees measured with increasing values counterclockwise from the 3 o&p12/G-codes/pages.html#39 clock direction (i.e. (b) If G16 has been executed to set a Polar Origin then for rapid linear motion to a point described by a radius and angle G0 X~ Y~ can be used. It is expected that cutting will not take place when a G0 command is executing.

This will produce co-ordinated linear motion to the destination point at the current traverse rate (or slower if the machine will not go that fast). The G0 is optional if the current motion mode is G0. (a) For rapid linear motion, program G0 X~ Y~ Z~ A~ B~ C~, where all the axis words are optional, except that at least one must be used.
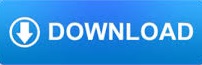